Optimizing Liquid Cooling in Data Centers
The Crucial Role of Coolant Distribution Units (CDUs)
The relentless growth of data consumption and the rise of power-hungry hardware have intensified the demand for efficient cooling solutions in data centers. Traditional air-cooling methods are struggling to keep up, paving the way for liquid cooling to take center stage. Within this paradigm shift, Coolant Distribution Units (CDUs) have emerged as critical components, ensuring the optimal performance and efficiency of liquid cooling systems.
Understanding the Importance of CDUs
CDUs act as the central hub of a liquid cooling system, responsible for circulating and conditioning the coolant before it reaches the heat-generating components. They perform several vital functions:
- Coolant Distribution: CDUs efficiently distribute the coolant to the servers and other hardware, ensuring even cooling across the data center.
- Temperature Regulation: They precisely control the coolant temperature, maintaining it within the optimal range for efficient heat dissipation.
- Flow Rate Management: CDUs regulate the coolant flow rate to match the specific needs of the hardware, preventing inadequate cooling or excessive pressure.
- Filtration and Purification: They filter out impurities and contaminants from the coolant, preventing corrosion and ensuring long-term system health.
- Monitoring and Control: CDUs provide real-time monitoring of critical parameters using devices like flow sensors to track flow rate, temperature, and pressure, enabling proactive maintenance and optimization.
Key Considerations for Optimizing CDU Performance
To maximize the efficiency and effectiveness of CDUs, several key factors warrant careful consideration:
1. CDU Capacity and Scalability:
- Accurate Heat Load Assessment: Accurately estimating the heat load of the data center is crucial for selecting a CDU with the appropriate cooling capacity. Oversizing can lead to energy wastage, while undersizing can result in inadequate cooling and performance degradation.
- Future-Proofing: Consider the potential for future expansion and increasing heat loads. Opt for a CDU with scalable capacity to accommodate future needs without requiring a complete system overhaul.
2. Coolant Selection and Management:
- Coolant Properties: The choice of coolant significantly impacts the system's efficiency. Consider factors like thermal conductivity, viscosity, and environmental friendliness. Water is a common choice due to its high thermal conductivity and low cost, but other options like glycol-based coolants may be suitable for specific applications.
- Leak Detection and Prevention: Implement robust leak detection mechanisms to prevent coolant leaks, which can damage sensitive equipment and disrupt operations. Utilize sensors, alarms, and automated shut-off valves to minimize the risk of leaks.
- Coolant Maintenance: Regularly monitor coolant quality and perform necessary maintenance tasks like filtration, purification, and replenishment to ensure optimal performance and longevity.
3. Pump Selection and Optimization:
- Pump Efficiency: Select pumps with high efficiency ratings to minimize energy consumption. Variable speed pumps offer greater control over flow rates, allowing for adjustments based on real-time cooling demands.
- Redundancy: Implement redundant pumps to ensure continuous operation in case of pump failure. This prevents downtime and protects critical equipment from overheating.
- Pump Placement: Strategically place pumps within the CDU to minimize pressure drops and optimize flow distribution.
4. Heat Exchanger Design and Efficiency:
- Heat Exchanger Type: Choose the appropriate heat exchanger type based on the cooling medium used (e.g., air-cooled, water-cooled). Consider factors like efficiency, size, and maintenance requirements.
- Surface Area and Material: Optimize the heat exchanger's surface area and material to maximize heat transfer efficiency. Utilize materials with high thermal conductivity and corrosion resistance.
- Fouling Prevention: Implement measures to prevent fouling (accumulation of deposits) on the heat exchanger surfaces, which can reduce heat transfer efficiency. Regular cleaning and maintenance are essential.
5. Control System and Automation:
- Intelligent Controls: Implement advanced control systems that can dynamically adjust cooling parameters based on real-time data like server utilization, ambient temperature, and coolant temperature. This optimizes energy consumption and ensures consistent cooling performance.
- Remote Monitoring and Management: Utilize remote monitoring and management capabilities to track CDU performance, receive alerts, and make adjustments from anywhere, at any time.
- Integration with Data Center Infrastructure Management (DCIM): Integrate the CDU control system with the DCIM platform to provide a holistic view of the data center's cooling infrastructure and optimize overall efficiency.
6. Energy Efficiency Measures:
- Variable Speed Fans: Utilize variable speed fans in air-cooled CDUs to adjust airflow based on cooling demands, reducing energy consumption during periods of low heat load.
- Free Cooling Utilization: Take advantage of free cooling opportunities when ambient temperatures are low enough to cool the coolant without mechanical refrigeration. This significantly reduces energy consumption.
- Heat Recovery: Explore opportunities for heat recovery, utilizing the waste heat from the data center for other purposes like heating or preheating water.
7. Regular Maintenance and Monitoring:
- Preventative Maintenance: Establish a comprehensive preventative maintenance program that includes regular inspections, cleaning, and component replacement to ensure optimal CDU performance and longevity.
- Performance Monitoring: Continuously monitor key performance indicators (KPIs) like coolant temperature, flow rate, pressure, and energy consumption to identify potential issues and optimize efficiency.
- Data Analysis: Utilize data analytics to identify trends, predict potential failures, and make data-driven decisions to improve CDU performance and reduce operating costs.
The Future of Coolant Distribution Units
CDUs play a critical role in optimizing liquid cooling systems for data centers. By carefully considering factors like capacity, coolant management, pump efficiency, heat exchanger design, control systems, and energy efficiency measures, data center operators can maximize the performance and efficiency of their CDUs, ensuring optimal cooling for their valuable IT equipment.
Incorporating these strategies not only improves the reliability and longevity of data center infrastructure but also contributes to significant energy savings and reduced environmental impact. As data centers continue to evolve and adapt to the demands of the digital age, CDUs will remain a cornerstone of efficient and sustainable cooling solutions.
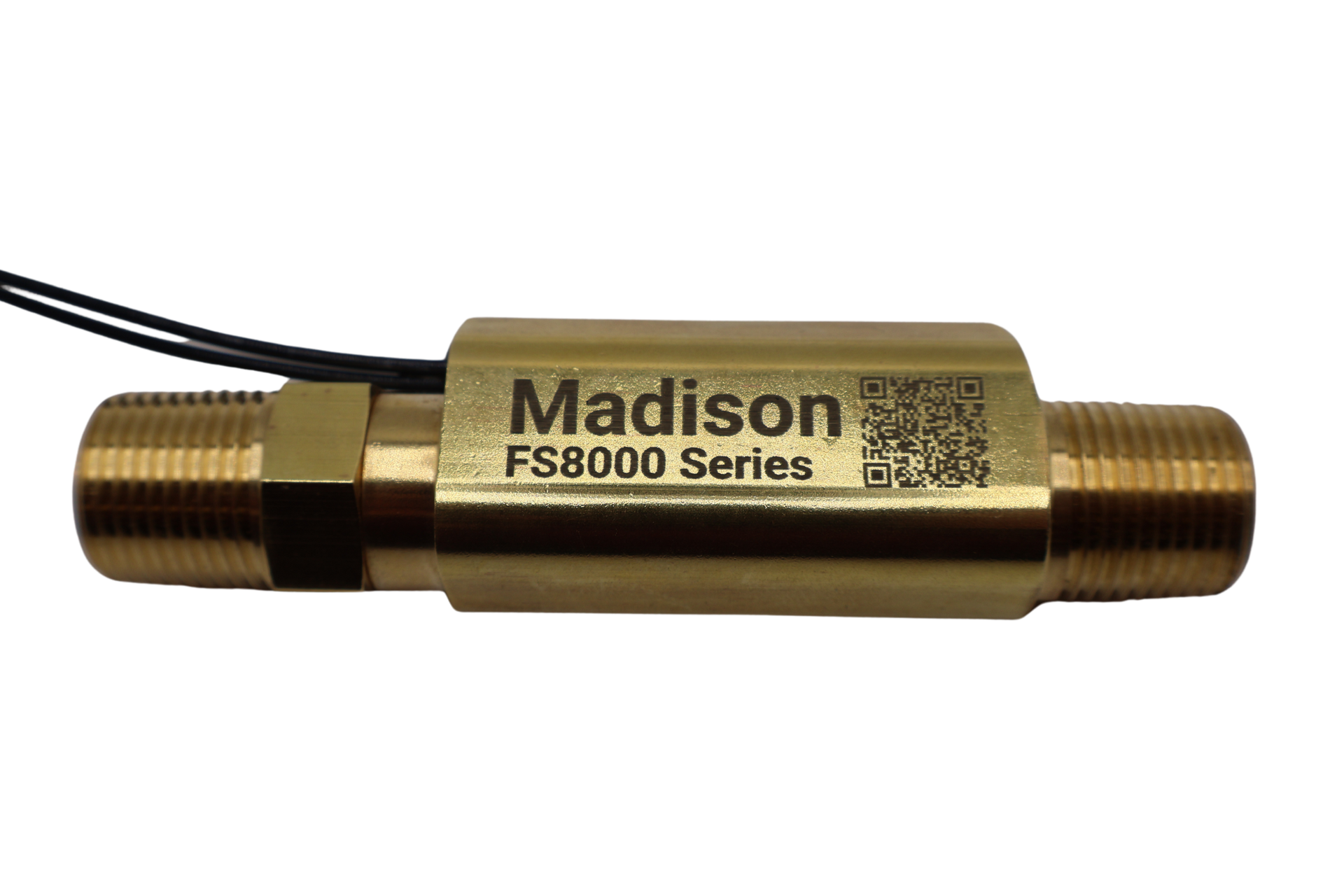
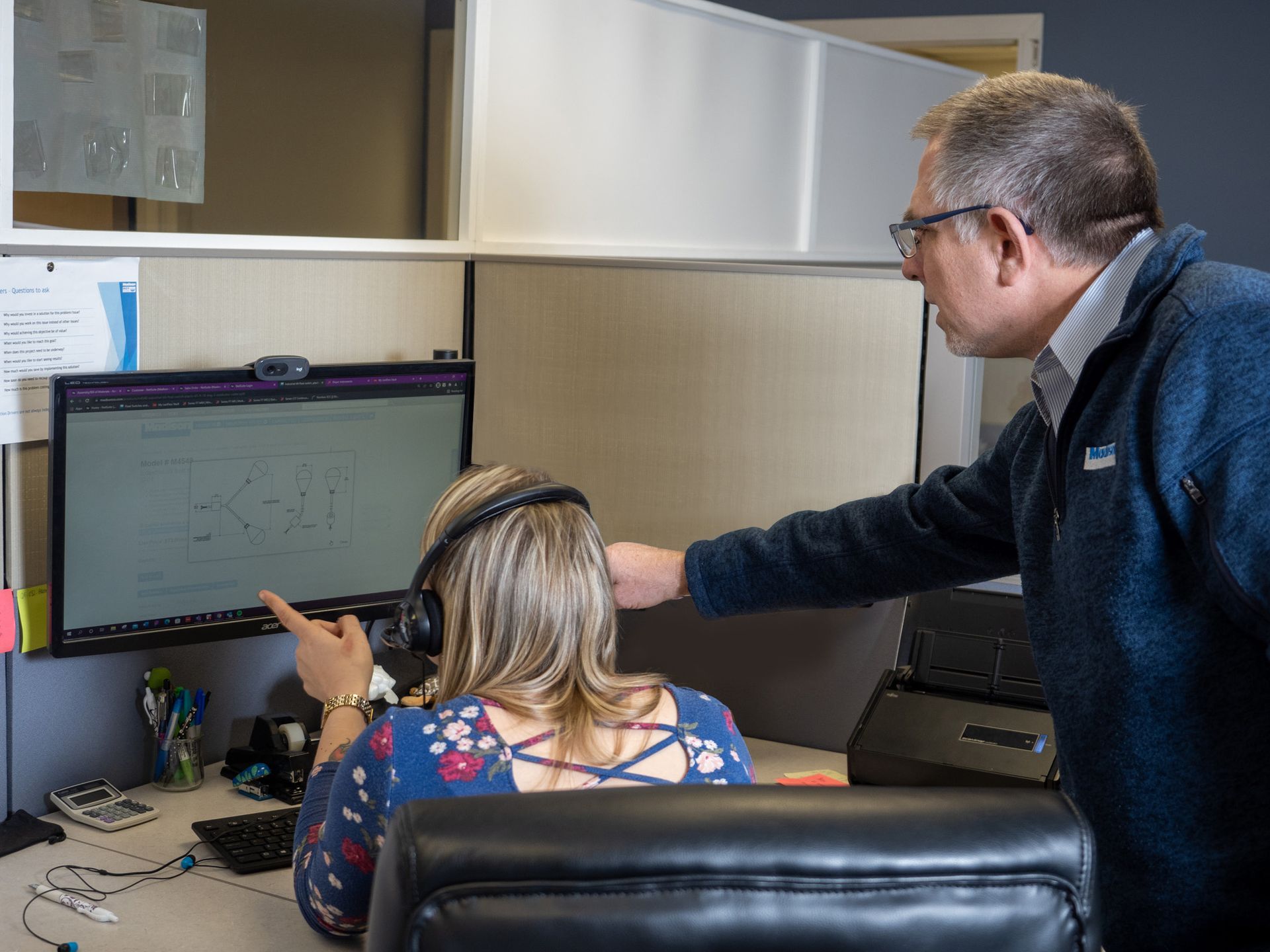